Flexo Printing Using Four Sustainable Packaging Materials
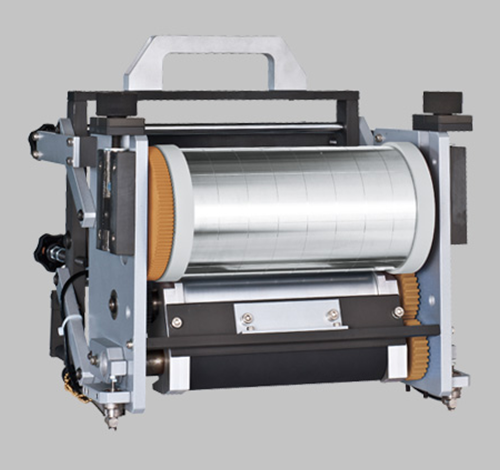
The packaging industry around the world is taking steps to become more sustainable and environmentally friendly. No one can release the flexographic printing market from these trends. As printing machines started to feel pressure from the customers to become more sustainable, it is vital to consider how and where to implement these changes.
Flexographic printing, often known as flexo printing, is one of the most popular packages printing technologies, for medium to long-term sustainable packaging. However, with an increasing number of customers preferring to do business with companies that include eco-friendly practices into their corporate strategy, it might pay off financially. You might be more deliberate about your sustainable packaging initiatives when it comes to flexo printing.
We will take a bird’s eye view of sustainable product packaging in this post. Also, we will see how a high-speed flexo printer helps any business’s environmental efforts. Here you can take a look at how you can use flexo printing in several sustainable packaging.
Flexo Printing Packaging Materials that are Sustainable:
A fine print job has four basic components, as every expert flexo printer knows. These are some of them:
- Substrates
- Image carriers and anilox rollers
- Inks
- Coatings and Adhesives
While these components are essential for the flexo printing process, there are ways to make sure about their long-term viability in terms of both your wallet and the environment.
Substrates:
Are you looking for environmentally friendly packaging materials? If so, substrates can be your choice! When it comes to substrates, there is a myriad of possibilities available by substrate suppliers:
- Bioplastics
- Recycled plastics
- Environmentally friendly recycled paper packaging
- Materials that are biodegradable and compostable
Don’t be concerned about specific plastic films as you can recycle the quantity at store drop-off points.
It is worthwhile to devote some effort to the design stage. Depending on your packaging, substrate manufacturers can offer you a variety of sustainable substrate solutions.
Note: Before you begin, double-check that the materials you are using have received approval for the product to be bundled. If you need to package something consumable, discover the most environmentally friendly materials for food packaging.
Other items may have less restricted environments. While sustainability is important, make sure that the substrate reflects the product as well.
Inks:
You can’t make a print without using a spot of ink. This is the first step toward a more sustainable flexo printing process. Use good ink options available.
Solvent-based inks must be avoided! These inks contain volatile organic compounds (VOCs). As these chemicals are dangerous, more precautions in the pressroom are required. This may suggest additional expenditures.
Electron beams or ultraviolet light have been used to cure some inks. These approaches are not as widespread as water-based ink, but hybrid inks are the way to go for flexo printers for those who need a solvent-free solution.
Hybrid inks combine the ease of use of water-based inks with the durability and dazzling shine of treatable inks. Using an electron beam to develop a system is expensive and also a long-term goal.
As not all image carriers are suitable for water-based inks, changing inks may cause some modification of your flexo process. Finally, the number of dangerous compounds reduced in the air and water make the redesign worthwhile.
Image Carriers And Anilox Rollers:
What type of image carrier do you use? Photopolymer? Do you think photopolymer plates are recycled and utilized in other plastic products? This is an excellent approach to reduce or eliminate the cost of buying new equipment.
Furthermore, photopolymer plates are not the most environmentally friendly option. Plates contain:
- Trace levels of lead
- Mercury
- Other hazardous substances.
When exposing the plate, these chemicals usually go into the drain. Submerging a sub-micro mesh filter in the wastewater disposal system will significantly reduce the environmental impact of photopolymer plates.
Rollers Made Of Anilox:
To maintain an equal ink spread on your image carrier, anilox rollers are required. They are also frequently composed of ceramic coating and steel. There aren’t many choices when it comes to eco-friendly anilox rollers, but it doesn’t mean you cannot do something!
As rollers come into contact with ink regularly, it is important to clean them, right? How you wash and clean your anilox rollers determines how ecologically responsible you can be.
Cleaning methods commonly use toxic chemicals that release volatile organic compounds (VOCs), causing the use of filtering devices and extensive capture.
However, there are certain methods for cleaning anilox rollers for flexo printing jobs that have little to no negative environmental influence. Consider cleaning with a water-based solution or cleaning with a laser.
Sleeves Made Of Elastomer:
Photopolymer plates can be replaced with an elastomer sleeve, which is a more environmentally responsible option. For long print runs, elastomer sleeves are made of high-quality rubber. Furthermore, elastomer sleeves ensure a high-quality print result, eliminating the need for a wasteful second run.
Sustainability entails more than just using environmentally friendly inks, substrates, and other materials. It’s also about making sure the flexo printing equipment is working to its greatest capacity. Elastomer sleeves keep flexo presses working for longer while also being:
- Long-lasting
- Easy and quick to clean
- Highly detailed
- Easy to install
Coatings And Adhesives:
Inks are simply one part of greening your flexo printing process. You will also want to make sure you are choosing environmentally friendly adhesives and coatings.
Synthetic coatings and adhesives typically emit more VOCs. As a result, you can use more renewable adhesive derivatives by sustainable designers.
Casein and gluten are examples of the most efficient adhesives. Some people avoid using animal proteins because they are their source. You can use plant proteins, such as maize starch or potato to make the most ecological and effective adhesives. Envelopes have reactive adhesives on the flap, you can activate by liquid and make the envelope sticky.
Also, think about how recyclable your adhesives are. Is it possible to decompose them without employing dangerous chemicals?
Conclusion:
In today’s business world, sustainability is a must-have feature. When it comes to flexo printing, sustainability has become an increasingly important topic. Taking advantage of this trend and staying on top of it will maintain any pressroom eco-friendly and secure.